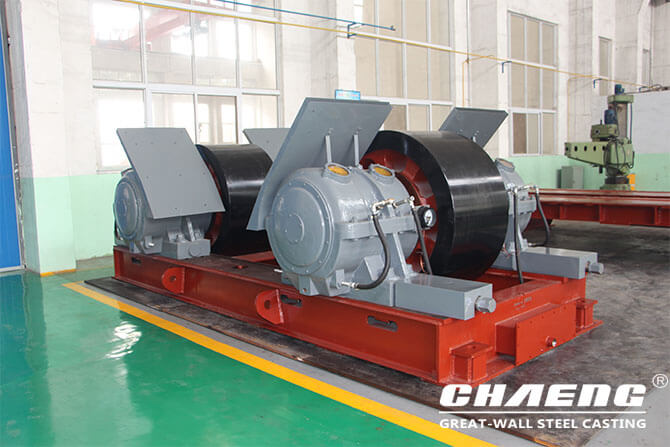
Making process of CHAENG kiln support roller
The first step: simulation, modeling
Prior to pouring, simulate the casting process by means of CAE software to analyze the modeling process, predict the quality and optimize the process. The metallurgical auxiliary equipment are well-equipped and the overall size is well controlled. Use water glass sand molding technology which can prevent the appearance of hot cracks in castings. At the same time, adopt pit modeling which is not affected by the seasons and has high production efficiency.
The second step: casting, heat treatment
Put the qualified raw and auxiliary materials into electric arc furnaces for smelting according to the proportion. Sample the molten iron for spectral analysis, and after passing the qualification, perform pouring process according to the principle of “low-temperature fast pouring”, and record the casting time and temperature.
The third step: polishing, flaw detection
Finally, cut the riser, flash, etc. CHAENG has a professional grinding and finishing team, large-scale shot peening equipment, which can effectively improve the appearance quality of the support roller, and make its surface finish meet the requirements of customers. It also uses advanced flaw detection equipment to perform non-destructive testing to ensure the internal quality of the support roller. Strictly prevent any defective products out of the factory.
CHAENG (Xinxiang Great Wall Steel Casting Co., Ltd)
Office Add: Mengzhuang Town, Huixian City, Henan Province, China
Postcode: 453600
Website: www.partscasting.com
Email: casting@chaeng.co
Tel: 86-371-55019878